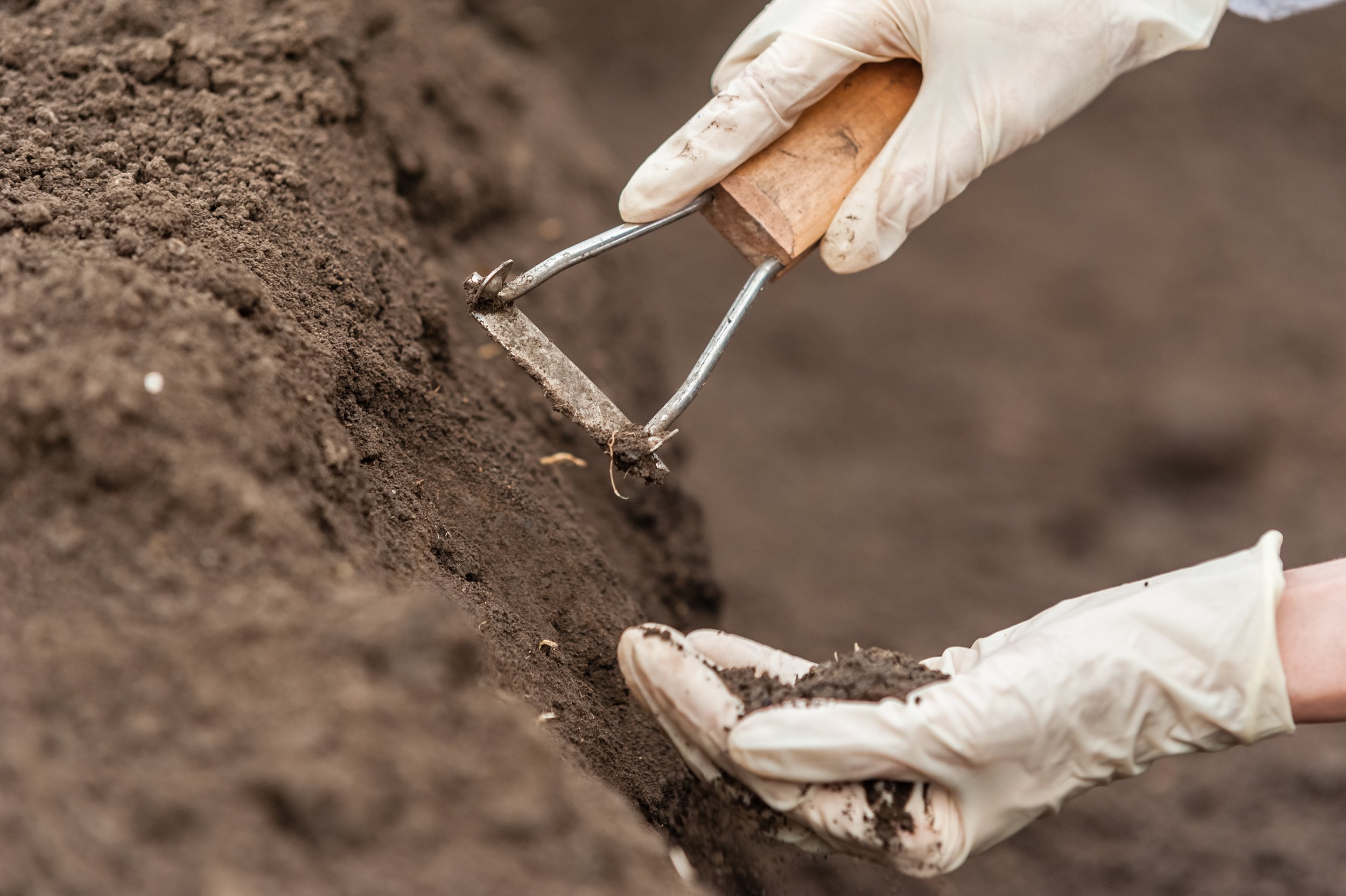
PFAS Remediation
Iron Creek & Jacobs Pilot Project
Project Details
Iron Creek Group partnered with Jacobs and Battelle to demonstrate that Tech Zero could remediate high concentrations of PFAS chemicals from soil using conduction and convection.
Project Operations
The feed soils were subsequently spiked with a 50:50 mixture of 3 percent Ansulite fluorotelomer-based AFFF, a 1999-era M3 electrochemical-based AFFF to bring the estimated total concentration of the 10 PFAS analyzed to above 40,000-ug/kg.
The mixed soil then was separated into several batches for treatment as follows: 482°C for 15 minutes; 593°C for 15 minutes; and 954°C for 30 minutes. Minimal removal occurred at the lowest temperature and 50 percent removal occurred at the middle temperature, both over 15 minutes duration. At higher temperature and 30-minute duration, all PFAS were removed to levels below the Limits of Quantitation, corresponding to an estimated mass removal of >99.9percent.
Planned Customer Results
350C was identified as the lowest effective temperature. This testing showed 99.4 percent
removal for the total of the 29 PFAS analyzed within two days at 350°C. Only 40 percent total PFAS removal was observed at 300°C over a four-day duration. Longer heating durations did not improve removal at either temperature.
​​The sulfonates (PFOS, PFHxS) are much more difficult to remove at lower temperatures but are very effectively removed at higher temperatures. Consistent with the ‘grouping data’ maximum removal is achieved after 2 days, at 350 C.
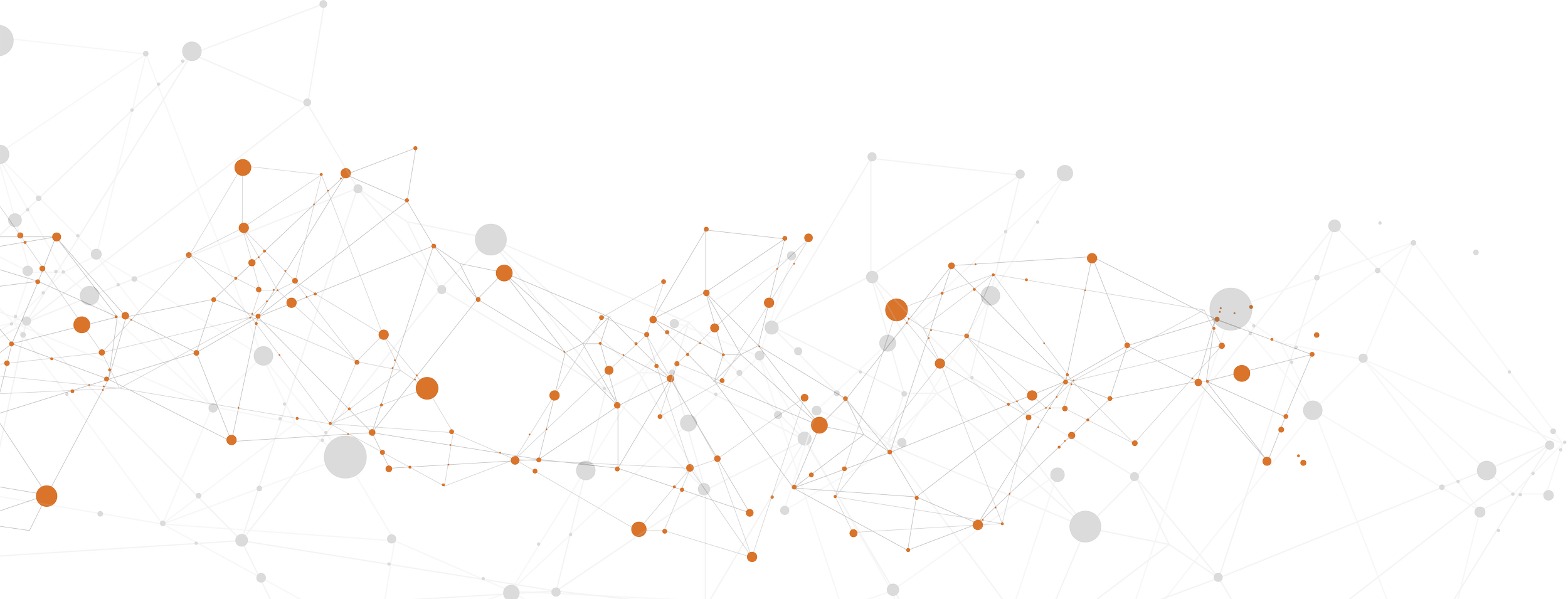
Department of Defense PFAS Pilot (Underway)
Project Details
The objective of the pilot is to demonstrate the effective treatment of soil contaminated with PFAS by thermal desorption and off-gas destruction using Iron Creek’s Tech Zero remediation technology.
Project Operations
Determine if it is possible to reduce the concentrations of PFAS in soil by >99%
The first objective of this field test is to validate Tech Zero’s ability to desorb and destroy PFAS contaminants in the soil. The success of this pilot is contingent upon the volume of mass that the unit can effectively treat within practical time frames and under specified temperature conditions.
Data Requirements
The technology performance will be evaluated based on contaminant concentration reductions in soil post-treatment, relative to starting concentrations. Soil samples will be collected and analyzed before and after each treatment run.
Post-treatment soil sampling results will indicate the amount of mass remaining in the treated soil (if any). These concentrations will be compared to initial concentrations to calculate the amount of mass removed.
Success Criteria
The objective will be considered met if post-treatment concentrations in soil indicate an overall reduction of PFAS in soil by greater than 99%.
Evaluate off-gas emissions
The second objective of this field test is to validate Tech Zero’s ability to destroy PFAS in the off-gas. Success will be measured by the amount of PFAS mass in the off-gas and the PFAS emitted from the test during each run. The modified TO-13 sample method (detailed in this plan) is designed to absorb any PFAS remaining in the off-gas, post-afterburner.
Data Requirements
Tech Zero’s off-gas treatment efficiency will be evaluated based on the total PFAS desorbed from the soil and destroyed by the Tech Zero’s afterburner.
Data required to quantify the total mass of PFAS in the off-gas stream will be a function of calculating the PFAS mass in the soil (pre-treatment), less the PFAS mass in the soil (post-treatment), plus the mass of the PFAS captured in the off-gas post-afterburner.
Success Criteria
The objective will be considered met if greater than 90% of the mass of PFAS desorbed during treatment is destroyed by the afterburner during treatment.
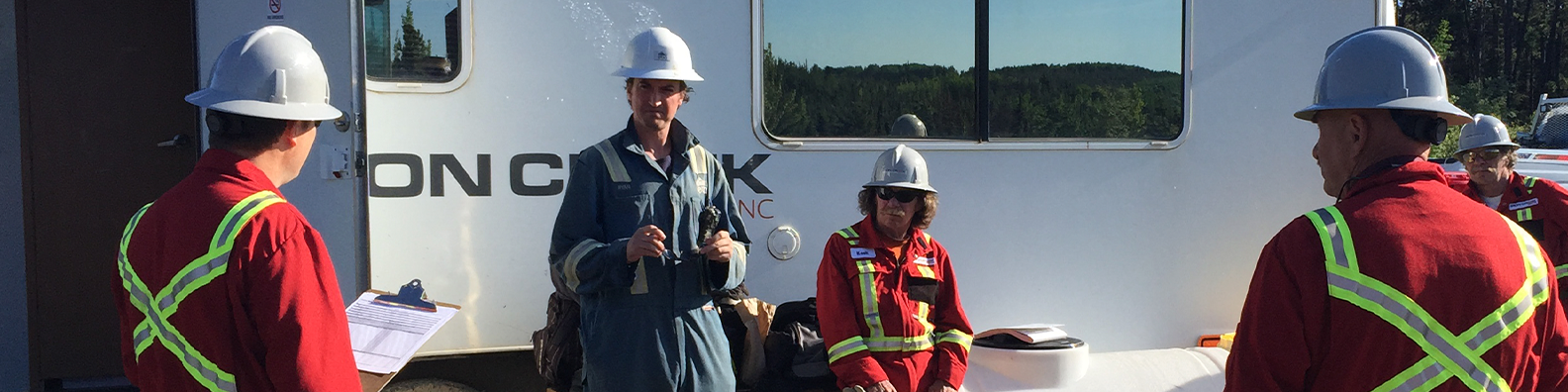
Safety is Our Number One Priority
Our process is designed to meet the most rigorous regulatory standards because we understand the biggest liability to site remediation is human health and safety. Our stringent protocols protect human and environmental health, and ensure an incident-free job site.
Even our technology is designed with safety in mind. For example, our remediation process is static— there are no moving parts. Contaminated soil stays in place, removing the liability associated with loading and trucking materials off site.
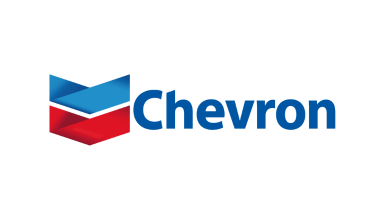
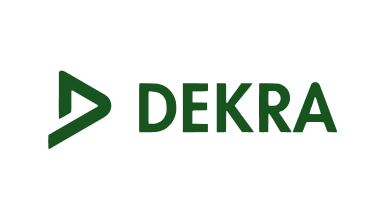
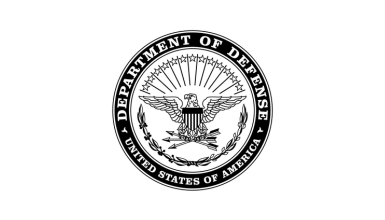
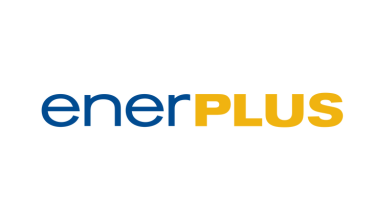
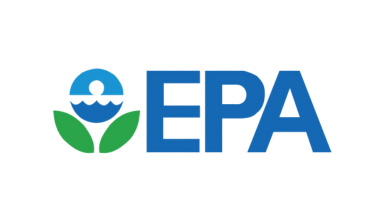
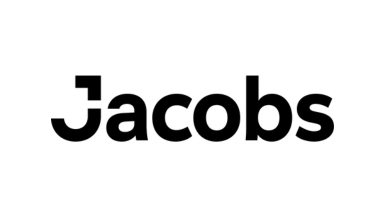
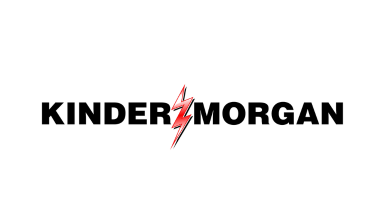
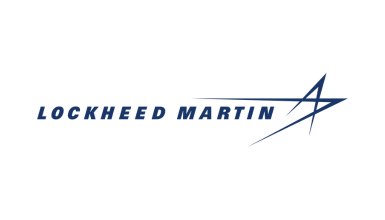
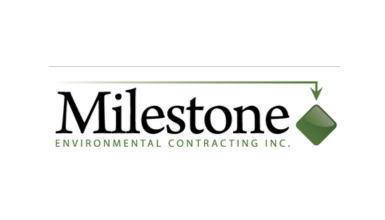
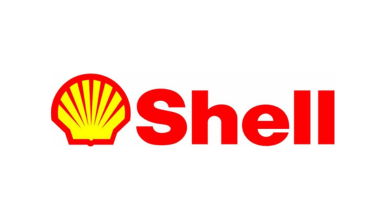
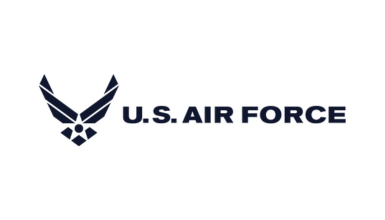
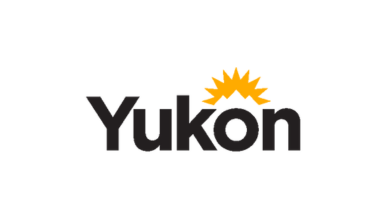
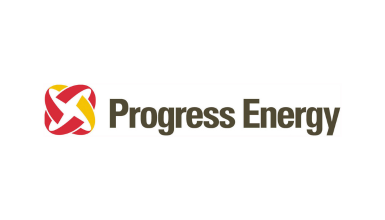
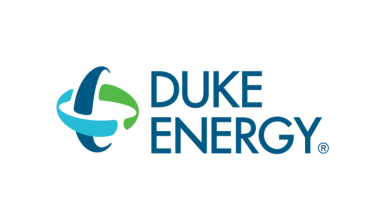
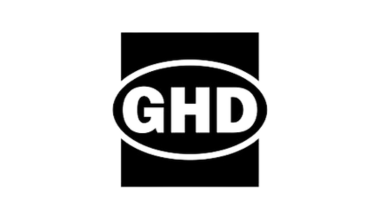
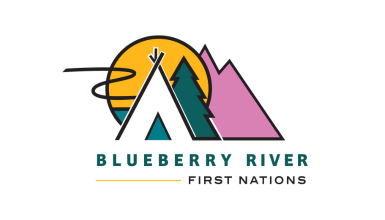
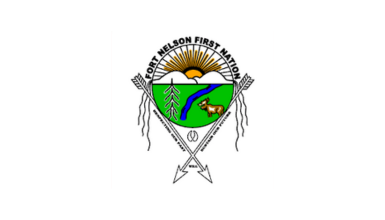
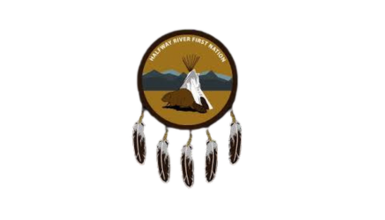
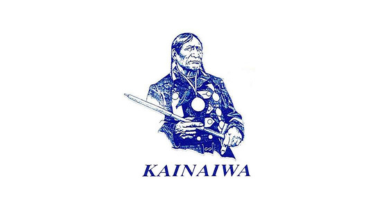
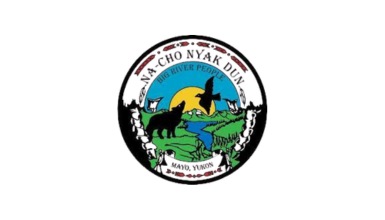
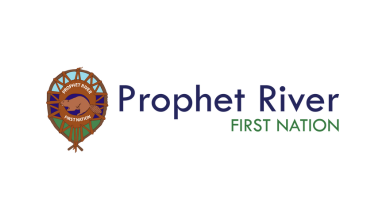
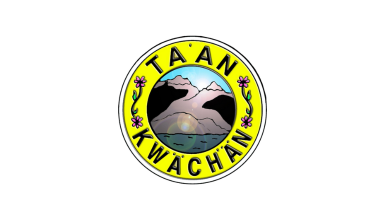
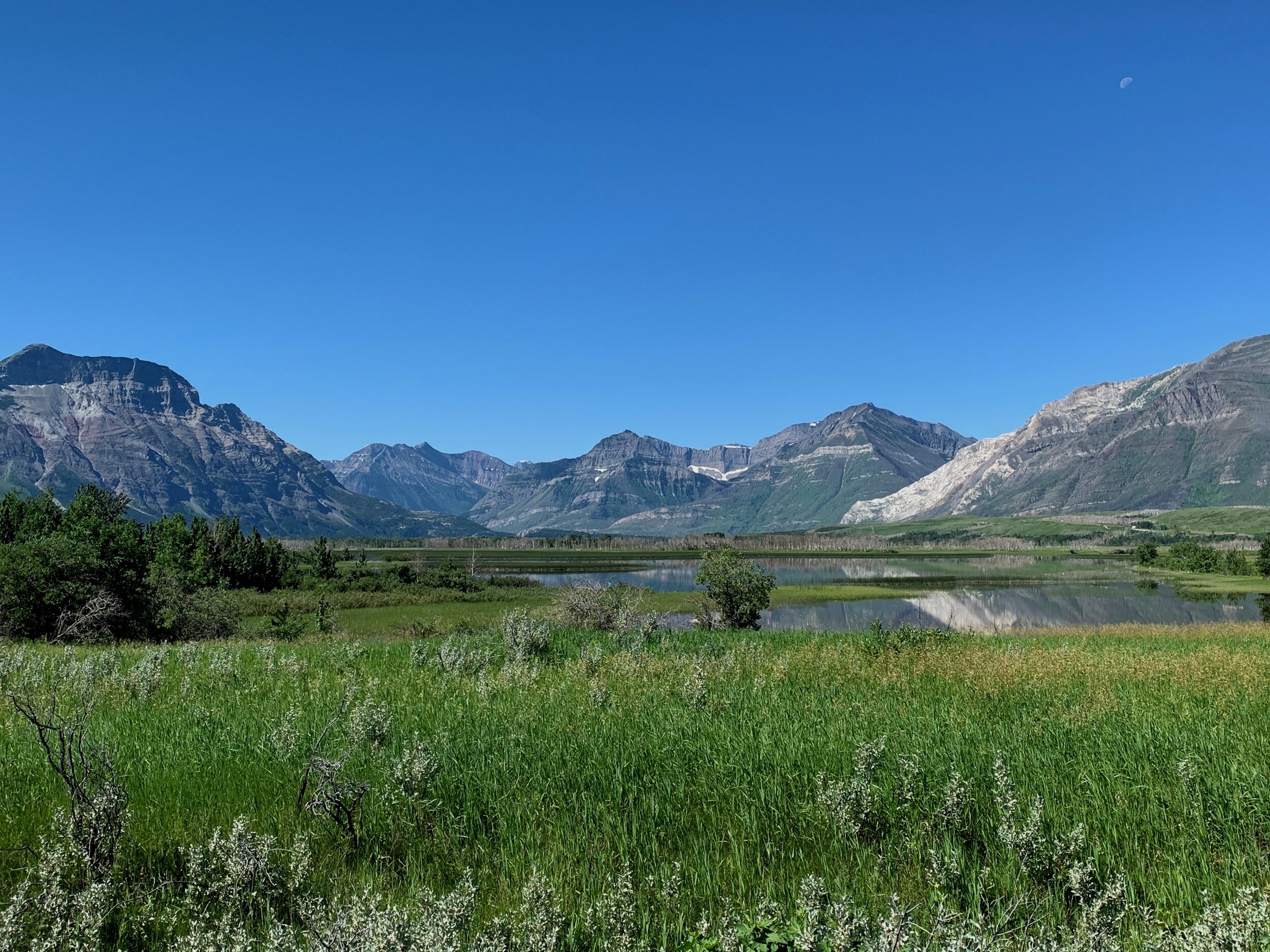